Lightweight Efficiency: Aluminium Fabrication in Modern Fuel Tanks
23 September 2024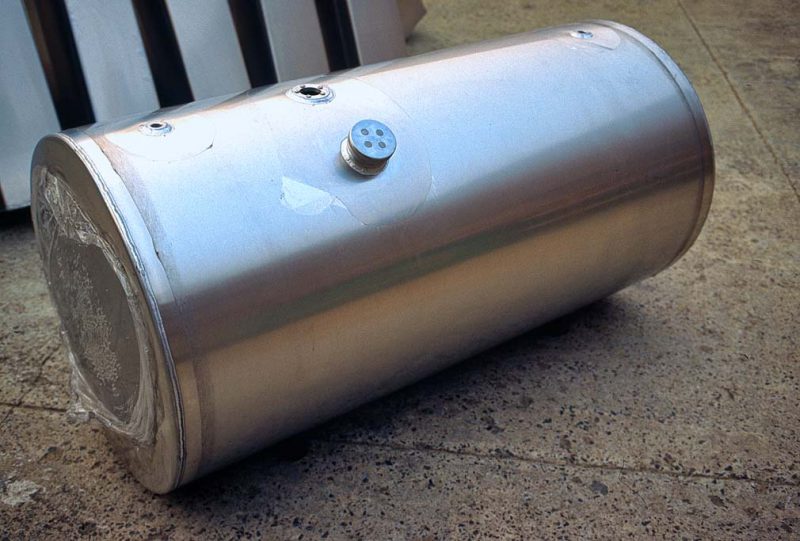
Round Fuel Tank SN1
Aluminium fabrication enhances efficiency and performance in modern fuel tanks. Explore the benefits of using aluminium in fuel tank design and construction.
Aluminium fabrication is transforming the design and efficiency of modern fuel tanks. By leveraging the lightweight and durable properties of aluminium, manufacturers are enhancing fuel efficiency and overall performance. This innovation not only improves vehicle and machinery functionality but also extends the lifespan of fuel tanks, making it a crucial advancement in the industry.
Advantages of Aluminium in Fuel Tanks
Aluminium’s suitability for fuel tanks can be attributed to several key characteristics:
• Lightweight Nature: Aluminium is significantly lighter than steel, reducing the overall weight of the vehicle or machinery. This weight reduction contributes to improved fuel efficiency and performance.
• Corrosion Resistance: Aluminium naturally resists corrosion, which is crucial for fuel tanks exposed to various environmental conditions. This resistance extends the lifespan of the tank and ensures reliable performance over time.
• Strength and Durability: Despite its lightweight nature, aluminium is strong and durable. It can withstand the rigours of high-pressure and harsh conditions, making it an ideal material for fuel tanks that require both strength and longevity.
• Thermal Conductivity: Aluminium has excellent thermal conductivity, which helps in managing the temperature of the fuel. This property is beneficial for maintaining optimal fuel temperatures and preventing overheating.
Aluminium Fabrication Process for Fuel Tanks
The process of aluminium fabrication for fuel tanks involves several stages, each contributing to the final product’s efficiency and reliability. Here’s a brief overview:
• Design and Engineering: The process begins with designing the fuel tank to meet specific requirements. Advanced software is used to create detailed blueprints and simulate performance under various conditions.
• Material Selection: High-quality aluminium alloys are selected based on their strength, weight, and corrosion resistance. Commonly used alloys include 5052 and 6061, known for their excellent properties in fuel tank applications.
• Cutting and Shaping: The selected aluminium sheets or plates are cut and shaped using precision tools. Techniques such as laser cutting or water jet cutting ensure accuracy and minimal waste.
• Forming and Welding: The cut aluminium is then formed into the desired shape using techniques like stamping or pressing. Welding is employed to join different sections of the tank, with methods like TIG (Tungsten Inert Gas) welding providing strong and clean welds.
• Inspection and Testing: After fabrication, the fuel tanks undergo rigorous testing to ensure they meet safety and performance standards. This includes pressure tests, leak tests, and inspections for structural integrity.
Why Choose Canfred Engineering for Aluminium Fabrication in Modern Fuel Tanks
Choosing a trusted aluminium fabricator like Canfred Engineering for aluminium fabrication in modern fuel tanks ensures several critical advantages. With a reputation for excellence and a track record of fabrication and supply of aluminium tanks, Canfred Engineering provides expertise in handling complex fabrication requirements with precision. Our experience and cutting-edge fabrication techniques guarantee durability and performance in every fuel tank. Contact us for more information.
Optimized by: Netwizard SEO